Create Your First Project
Start adding your projects to your portfolio. Click on "Manage Projects" to get started
"Integration Style" Drivetrain
Project Type
Class Project, Machine Design
Date
March 2022
Team Members
Andrea Francis, Darius Soo Hoo, and Shweta Raje
My role
Worked on the analysis of forces on individual components such as the gears, and the shafts used in the design
Location
University of Denver, Denver, CO
Goal: Apply Machine Designs concepts learned through the class to a realistic project.
My team decided to design a drivetrain for a wheeled rover vehicle.
The design chosen is a drivetrain of an “Integration-style” Rober Vehicle. The entire rover is made of an aluminum chassis with four wheels and four motors, and weighs 12 lbs. The drivetrain chosen for one wheel and one motor consists of two shafts, two gears, two mounted roller bearings, and two high load shielded ball bearings. The shafts are made of 1045 Carbon Steel and are each different lengths depending on what they are connected to. The longer of the two shafts is 5.5 inches long and connects the chassis to the pinion gear and the wheel. The wheels weigh about .45 pounds. The shorter shaft is 3 inches long and connects the chassis to the driver gear and the motor. The motor provides a torque of 40 lb.in and weighs approximately 2.5 pounds.
Conclusion/Results:
After analyzing the integration drivetrain’s gears, shafts, and bearings mechanisms including interference fits and key analysis, it was determined that the overall drive train and all its components will be safe to operate for the required torque of 40 in-lb. With all the safety factors being over 1, the drivetrain was determined to not fail under fatigue, shear, and torsional forces. The 1045 Carbon Steel Shafts guarantee the physical integrity of the system. The bearings cover the rover’s rpm requirements with ease since they have an rpm limit of 5000 and 22000 rpm.It was determined that it was in the team’s best interest to use a key for the gears and shafts since the safety factor of the key was 8.278 versus 1.28 and 1.16. Overall, the drivetrain will be able to support the operation required under the given conditions while having no failure in any of the components.
Takeaways/Lessons:
There are many improvements that can be made to this design, especially when considering individual components.
1. More consideration could be made of how the wheel would attach to the shaft.
2. Some discrepancies were made when calculating the interference fit, another stress concentration should have been used in this case
3. Different sizes for the components could be analyzed to determine better functionality
What did I enjoy?
I really like how I was able to work on a project with my team members and that it involved us coming up with the design and configurations based solely on the requirements given. I was able to learn how intricate designing for specifications was.







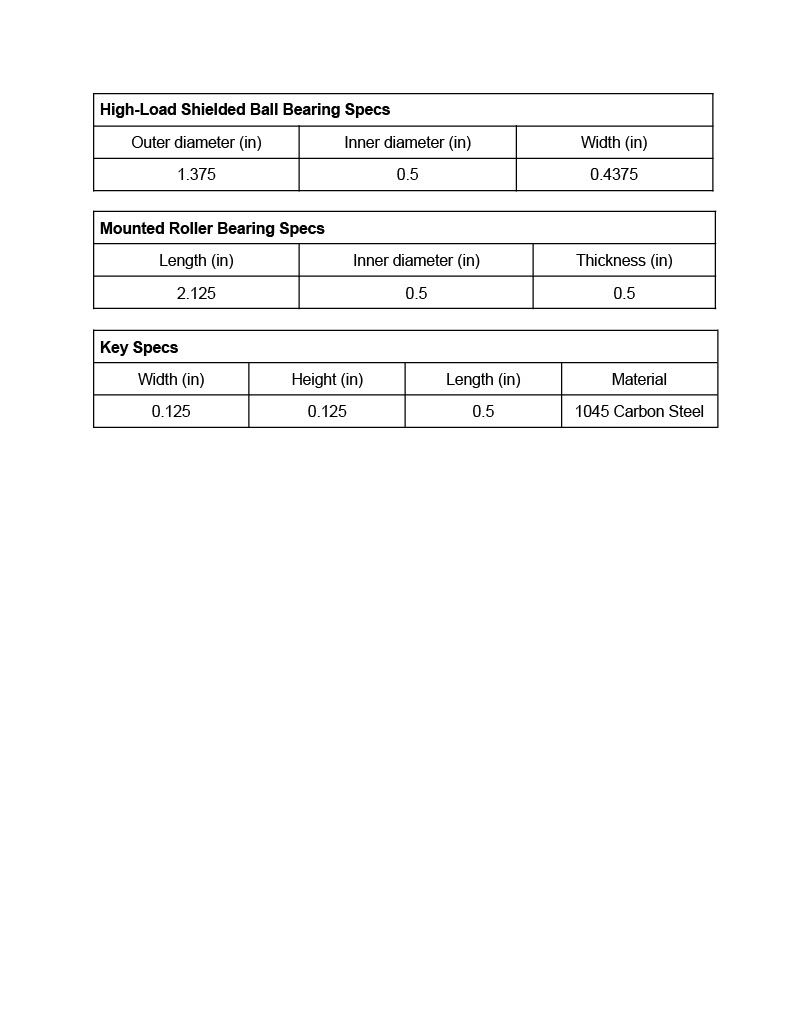















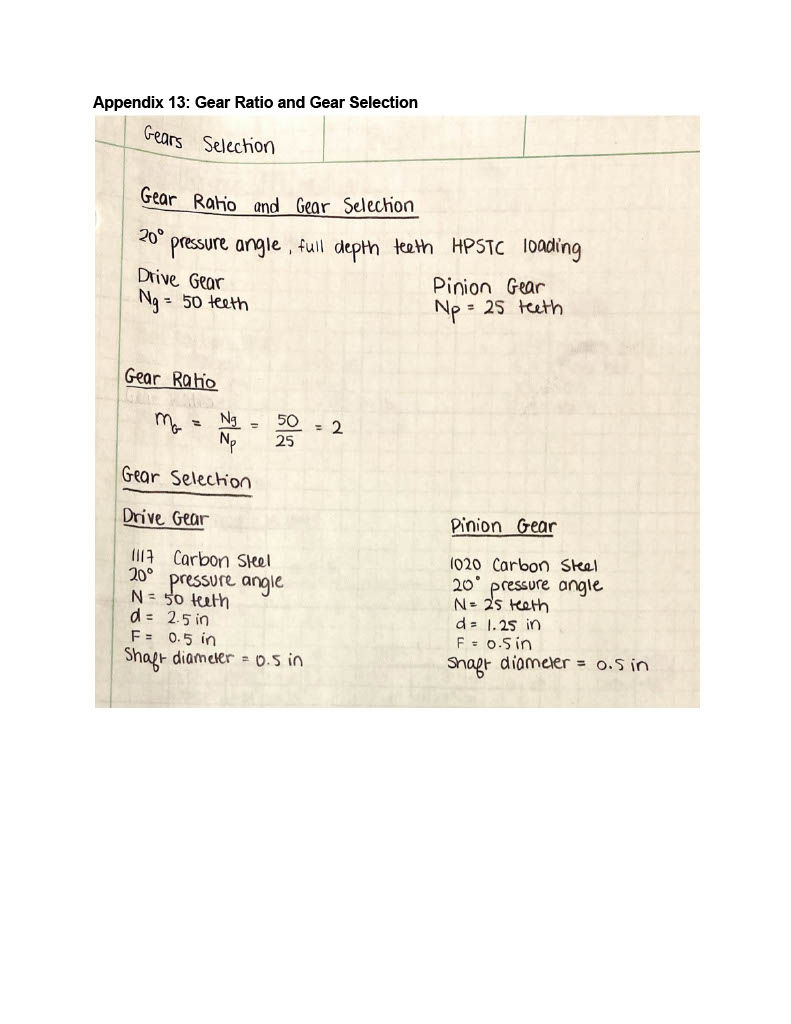











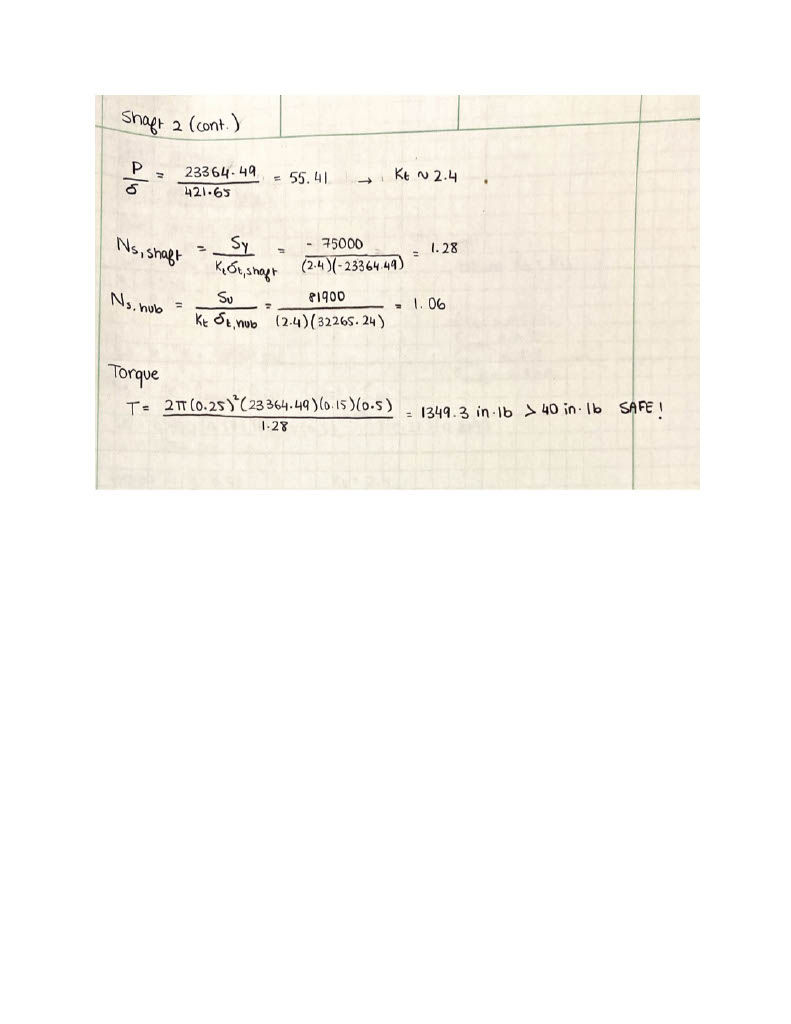

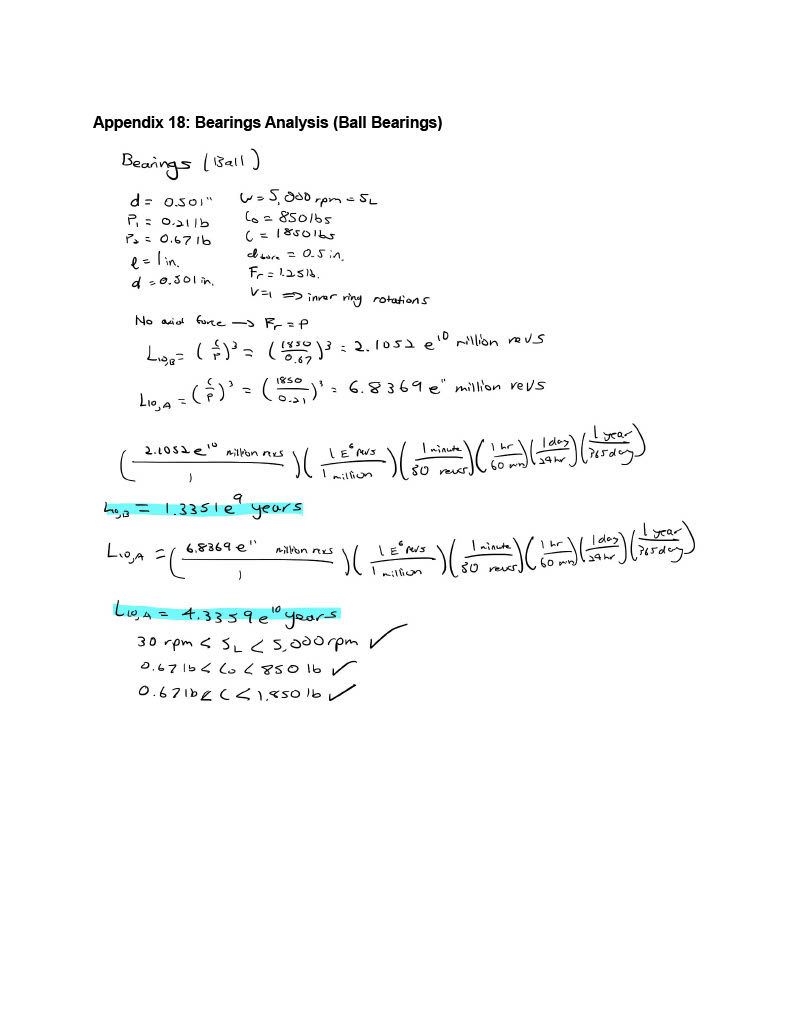





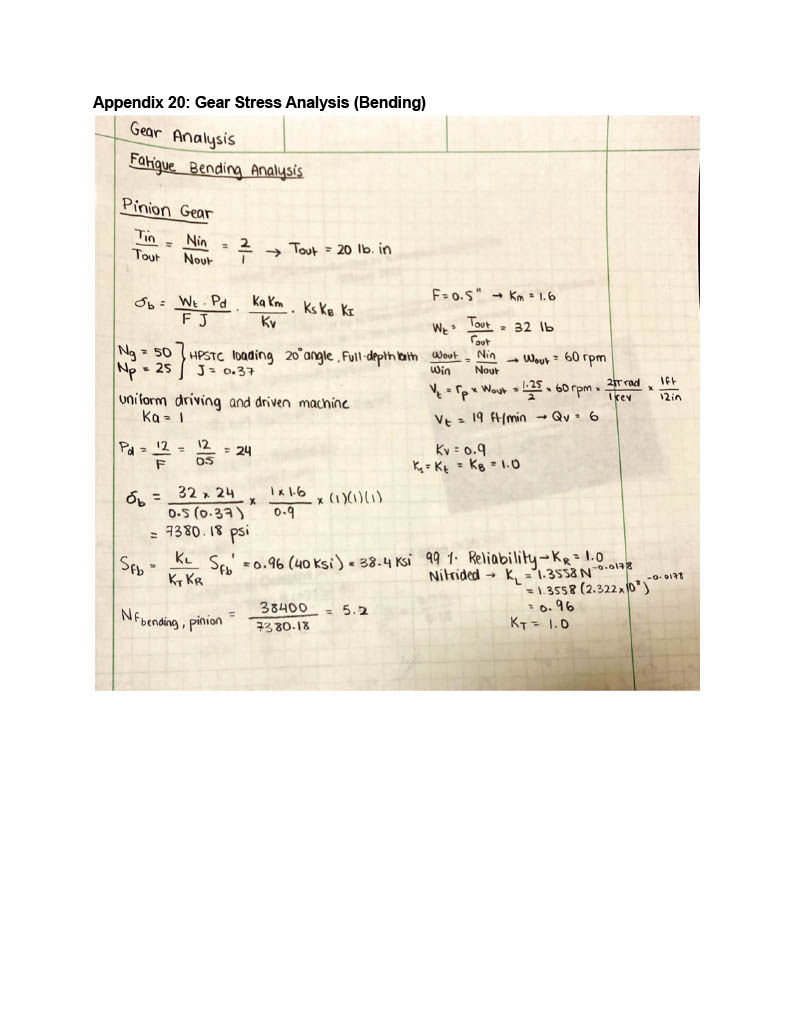